Rubber flooring is not rocket science, but …
14. April 2022
Drive a heavy load into an Earth orbit by means of a jet engine where the injection of a propellant mixture based on a high-pressure liquid fuel and a high-pressure liquid oxidant initially maintained at cryogenic temperatures to keep it liquid and optimize their density and then turbo pumped to end up on a combustion chamber where they are mixed in a sophisticated way to achieve an efficient combustion with very high temperature, that all the components must withstand without shrinking, sounds very difficult. If you disagree look below at the simplified block schemes of such full of pipes rocket engine.


But we should not minimize the challenges behind any activity you make and to understand that there is a lot of science, physics, and experience in the simpler activity you may work on. The better knowledge and experience you have about this science behind; the best will be the quality of your job.
This long preliminary is to explain that in our safety surfacing business we have also some technical challenges that the installers should master to get the best results.
In your job sites you are managing a chemical plant outdoors without too much control on the environment, and you are mixing several chemicals that interact among them and with the environment to achieve a good flooring performance if all goes well.
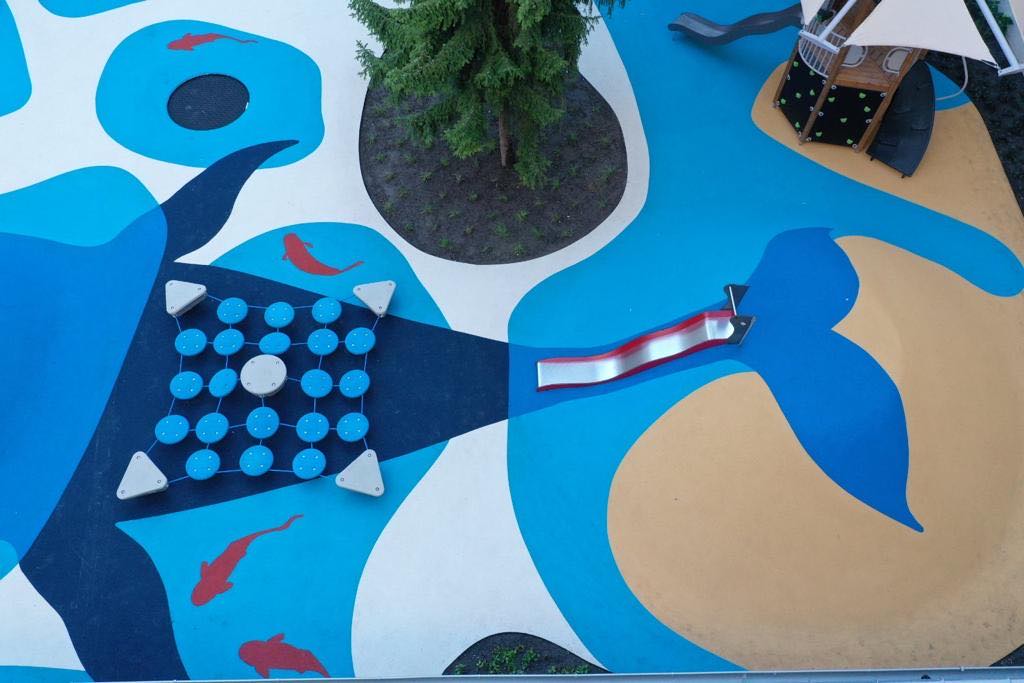
These are some of the main things you must do:
- Check the weather forecast on the days of your planned installation.
- Check the status of sub-base, drain and edging before starting installation. Is it compacted enough? is there new asphalt or concrete? Is already dry enough? Is drainage correctly made?
- Keep a register of everything as a quality control, including batch data, pictures, weather data and all potentially useful information in case somebody need to do an audit or open an investigation of the cause of a future problem.
- Keep the materials protected from moisture or extreme temperatures on your warehouse or on site before or during your installation.
- Select the most appropriate PU binder, curing behaviour and viscosity for the expected weather conditions (temperature and humidity).
- Prime the edges, play equipment or furniture foot and concrete or asphalt sub-bases to ensure the best gluing of the flooring.
- Careful measure the binder proportions recommended by the manufacturers.
- Keep the mixing times recommended and visually check the mixing was appropriate.
- Ensure the thickness of the different layers is according to the specifications by using screed rails or other equivalent tools or methods.
- When finished, ensure to protect the access to the area to persons or animals before curing is fully achieved and keep the recommended curing time before opening the area.
By the way, getting back to the top of this article, maybe you will never be in a team to lift off a space rocket and place a payload to orbit, but if you are working at the Playground and safety flooring business you will also have technical challenges to face, lessons to learn, and you will be able to enjoy a lot as we do.