How to design the wet pour safety flooring of a playground to fit the available budget
30. June 2022

Introduction
In the implementation of a playground there are three main work items that round off the total budget. They are as follows:
- Civil works of land preparation for the area, such as excavation, levelling, compaction, installation of perimeter edges and fences (around 5-15% of the total budget).
- Safety flooring for shock absorption (for wet pour would be typically 35-50% of the total budget).
- Supply and installation of children’s play equipment including safety certification and test of the area (around 50-60% of the total budget).
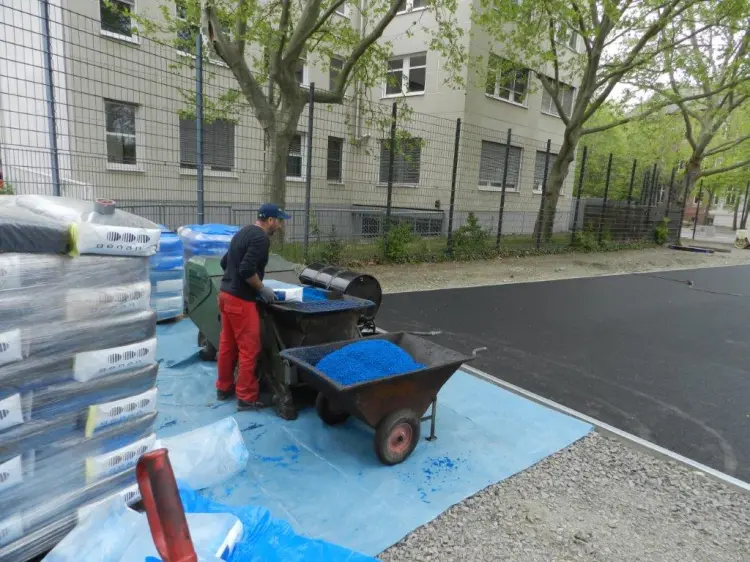
Very often, the developer or owner of the area has previously decided certain issues such as the type of safety flooring they want to use, based on previous experiences or the types of playground equipment planned and what is the proportion of the total available budget they intend to dedicate to the flooring.
Generally, the priority is to maximise the amount of playground equipment available to suit the intended number of users, so that the amount available for the flooring is often subject to limits that we must be adhered to.
If you are a playground designer or landscape architect, your decisions have a decisive impact on whether these budget limits are feasible.
See on the next few chapters the main factors you must consider.
Various Fall Heights in children’s play equipment:
Playground equipment has various maximum fall heights that determine the Critical Fall Height (CFH) value that the rubber surfacing must protect. These fall heights can range from a maximum of 3.0 m to a minimum of 0.60 m. (Requirements of the series of norms EN-1176-XX). A sophisticated play structure will have different fall heights at different parts of the structure.
Making the flooring for the necessary thickness to protect the maximum range of fall heights in the entire area is impractical because it would be very expensive, so the thickness of the flooring must be adapted to the different fall heights of the different parts of the play equipment.

Play equipment is normally distributed in areas determined by the age ranges of the children, but the final distribution and orientation of said equipment to optimize the areas of different fall heights must be considered because it will have a significant relevance in the total m2 required, of the different thicknesses and therefore in the feasibility of being below the budgetary limits established for the safety surfacing. Simply twisting of a play structure can mean a significant increase or decrease in certain thicknesses when combining the safety areas of them that are established at the various EN 1176 standards.
Sub-base types:
When the sub-base is a concrete slab, the different necessary fall heights and therefore the different flooring thicknesses must be carried out avoiding steps, so additional amounts of flooring material will be required to make accessible slopes that avoid said steps, which would mean an additional risk of trip and fall or difficulties for wheelchair and other users with some mobility disabilities.

If the sub-base is made with compacted crushed stone, the necessary thicknesses can be adjusted so that the upper part of the flooring is completely flat, and it is possible to have the different flooring thicknesses necessary for the CFH that are needed.
Types of perimeter edges:
We can recommend different types of perimeter edges such as bricks, concrete edges, aluminium or steel profiles or cuts and grooves in the concrete slabs. You should never use timber or other shape of wood. One of the most frequent warranty problems that requires repairing flooring is the separation of the rubber flooring from the edges of living materials such as wood logs, which vary in shape and dimensions depending on environmental conditions as temperature and humidity.
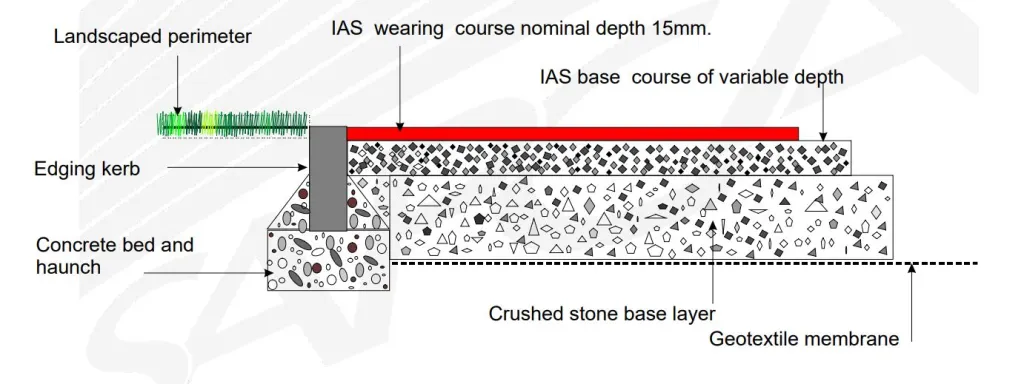
Drawing from the SAPCA Code of Practice for the Installation and Maintenance of Wet-pour Safer Surfacing for Playgrounds
Virtually all suppliers of flooring materials currently exclude this type of edge in their warranty conditions.
Mixing different types of surfacing:
It is a common practice for different play areas to also have different types of safety flooring to better match the type of equipment. For example, areas with sand or wood bark next to others of rubber safety surfacing. Pay attention about how to avoid problems if you do this.

If your design includes these types of mixed surfacing solutions, maintain a good separation or enough distance between the areas of sand or other loose materials with the areas of continuous rubber flooring. The remains of sand or other loose materials, will end up moving to the rubber flooring area, generating high maintenance, and cleaning costs and wear and tear on the top layer of the rubber flooring, reducing his lifespan. If they must be adjacent, please include enough perimeter edge to minimise displacement of loose materials over the rubber.
Choosing the colours of your design:
One of the advantages of rubber flooring is the possibility of using multiple colours and 2D or 3D graphics on the top layer of the flooring. The bottom layer that provides the absorption capacity has a variable thickness depending on the required Critical Fall Height (CFH).
The choice of colours for this top layer is of relevant importance to the total budget of the flooring.

Certain colours have a higher price per Kg due to the difference in production costs of certain dyes and the amount of necessary colour stabilisers to protect the granules from the effect of UV rays.
Since about 12-13 Kg of granules are used for each m2 for a thickness of the typical top layer of 15 mm, a simple price difference of € 0.10 per Kg ends up representing a significant difference per m2 of € 1.3 and for an area of 500 m2, it alone represents a difference of € 650 in material cost.
But that is not the most important extra cost, certain colours cannot use conventional aromatic binders, as they are not UV resistant and therefore produce an amber or yellowing effect as a film on top of the granule, turning a light blue colour into a khaki green.

These special colours require to use a special aliphatic binder whose additional cost per Kg can easily be from 5 to 7 € and considering an average binder proportion of 22% they mean an additional cost per m2 of 18 € and for the same example of an area of 500 m2 it would be an additional cost of materials, only due to the binder effect of 9.000 €.
Added to the cost of the granules, a different choice of colours can mean an additional cost of 20/25 € per m2.
The colours that require special aliphatic resins (for example, our CONIPUR 4080 or CONIPUR 4090) appear in the following table:
