Techniques for good colour transitions on EPDM top laye
30. June 2022
One of the great advantages of wetpour (pour-in-place) rubber surfacing is the potential for using designs with different colours and all kind of shapes and graphics.
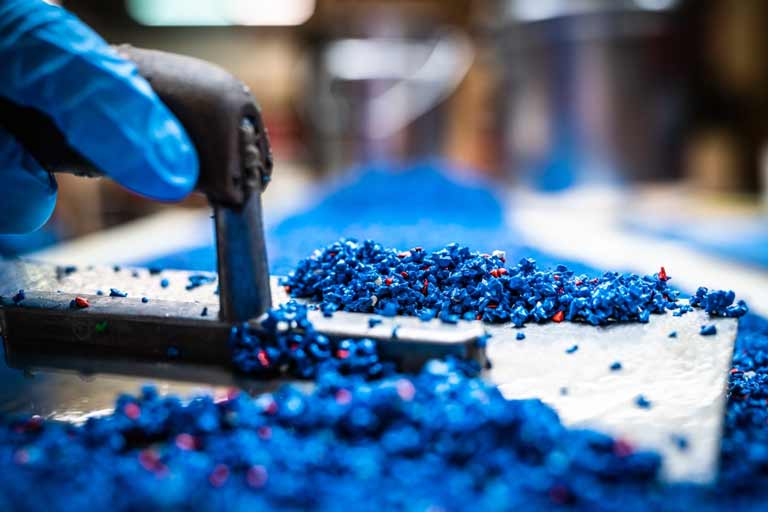
Where a seam is necessary, there is a potential for joint to fail at some future time, so it is important to ensure that construction joints or overnight joints are kept to a minimum. Construction joints are, sometimes however, a necessary part of the installation process and unavoidable when using areas or graphics with different colours.
Essentially the main challenges when using different colours are:
- To get a sharp and clean transition between colours.
- To avoid a mid-term separation of the lines between both colours laid at different time with one of the colours already cured.
Cracking, splitting or separation of joints of different colours is an indication of a bad installation technique and is not acceptable.
All installers we have met have been able to develop their own techniques and “know-how” for these colour transitions. The ones that follow are the most common ones we have seen during the last few years.
Techniques for joints of different colour
Wet on wet transition
This is one of the techniques requiring good skills and a lot of experience. It is difficult to get a sharp and crisp colour transition without some granules of one colour invading the other one. The main advantage of this technique is that there are no problems of line splitting because the granules of first colour are still sticky when laying the new colour.

It is done while the first colour is still not cured, and the binder is sticky on the granules so that when laying the new colour and pressing with the trowel the joint is perfectly glued. Pressing is essential for a good seam and the main difficulty is avoiding some granules to contaminate the other colour, so that the transition line may be irregular.
Cutting transition
This is one of the most common techniques. The line achieved is crisp and nice, but it is essential to prime very well the colour edge after cut and before laying the second colour and also use some cutting tricks to avoid short or mid-term line splitting.

The kind of cutting is important to get a good overlap between the two colours. Some installers do the cut on an angle to inside or outside or in a step form and some do a partial cut, ripping the sliced part and allowing some rest of the first colour to keep attached to the base layer what will improve integration with the second colour avoiding at the same time the seam splitting.
Film transition
Some installers use a transparent plastic thin sheet of Polycarbonate, Acrylic, or a similar thin film of plastic material after finishing laying the first colour. For a 15 mm top layer they would use a film of a height of 40 or 50 mm. They would then lay the second colour and when both are fully cured, they would just cut the leftover of the plastic film.
The colour transition will be sharp without any granule’s contamination between the colours. We have no evidence about long-term line-splitting risk of this technique but apparently it seems to work pretty well.
Shaped moulds for Patterns
It is possible to inlay patterns of different shapes and colours within the wet-pour surface to improve the ‘play value’ of the surface and the aesthetics of the project.

These patterns of contrasting colours may be achieved by using shaped moulds of the same thickness as the top layer and are usually manufactured from plywood or polystyrene. The basic colour of the top layer is installed with the mould in place and, when this layer has cured, the mould is removed, and the contrasting colour is trowelled into the shape left by the mould.
To avoid line splitting, the installer must ensure that the joint between colours is properly primed and compacted.